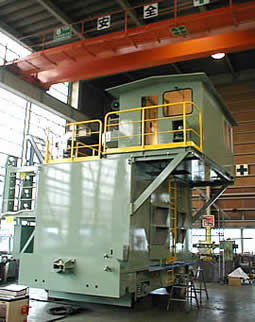
Quench Electric Locomotive (QEL)
A Quench Electric Locomotive (QEL), which moves between the furnace and quenching tower, is used for quenching coke in a coke oven plant. The QEL is powered by a pantograph system driven by a motor.
Diesel Electric Locomotive (DEL)
DEL is a locomotive which hauls the freight car in the plant. It has excellent fuel efficiency and low maintenance. The DEL has a diesel generator which powers the traction motor.
Compatible with human beings and environmentally friendly, by changing from hydraulic pressure control to electrical control
TMEIC has developed a Diesel Electric Locomotive (DEL) by applying the experience of 100 years of rail car engineering, - “Committed to people, committed to the future”.
The Diesel Hydraulic Locomotive (DHL) is currently used in steel plants, for the transportation of heavy loads and hazardous materials. To meet customer requirements for an environmentally friendly design, good fuel efficiency, and easy maintenance, TMEIC proposes a diesel electric locomotive applying a new drive system. In addition, DEL achieves increased maintainability and reduced service parts.
Features of the diesel electric locomotive
In DHL, the hydraulic gearbox is driven by the engine, and the power is transmitted among the reversing gear, screw shaft, and reducer. In DEL, the engine rotates the generator producing the electric power directly. The DEL locomotive is 20% more efficient than the DHL locomotive. The DHL uses 22% of the diesel fuel energy for output while the more efficient DEL uses 27% of the fuel.
The diesel electric locomotive has three additional outstanding features:
- Fuel efficiency - By using an inverter in the drive system, fuel consumption is reduced. In addition, by using one generator for driving and one for auxiliary functions, greater reduction of fuel consumption is expected. Also, environmentally, it contributes to a reduction of black smoke, COx, and NOx emissions.
- Easy maintenance - By reducing the hydraulics system as much as possible, the need for special maintenance skills is limited. In addition using standard electrical devices, maintenance programs are simplified. Further simplification results from reducing the number of devices that are used.
- Cleanliness - By changing the drive system from hydraulic to electric, the hydraulic equipment is eliminated so there are no oil spots and the locomotive is kept cleaner.
- Drive engine and auxiliary engine
The DEL is more fuel efficient because the drive engine is stopped when the locomotive is idling. In addition, because it is a general-purpose diesel generator, it can receive standard maintenance from the engine manufacturer. - Inverter
Inverter drives are used and contribute to energy savings. Also an electrical brake can be applied, reducing mechanical brake pad wear. - Brushless generator and electrical motor drive
Brush maintenance is not needed, and the drive generator is sealed to protect it from the environment. - Spring drive disk brake
There is no-wear on the wheel treads, and the fail-safe brake can be actuated by air pressure. In addition, the parking brake can be used so manual brake operation is not needed. - Apply Room type to car body construction
The car body and frame structure is furnished in a room type enclosure to allow equipment to be protected from the weather, with an access aisle for maintenance. - Noise-reduction
Noise-reduction is achieved with a sealed engine room and adoption of the electric brake. - Reduction of maintenance parts
A smaller number of parts, such as the subsidiary generator, V-belt, brake, air parts, and reducer, are required. - AC100V, AC200V power plug
By using the auxiliary diesel engine generator, general electrical equipment can be employed in the locomotive.
- Drive engine and auxiliary engine
Future plan for unmanned operation
- Implement automatic control for constant speed running to adapt to changes of rail track condition.
- Control the electrical braking force to improve the accuracy of stop position control and reduce the number of inching operations.
- Create a uniform braking distance for each locomotive with the electrical brake.
- Adopt start-up acceleration to allow for proper traction load and perform effective travel and brake control.
- Implement automatic speed control of the drive electrical equipment through accurate detection of Anti-Slip and Skid Change with the use of automatic sand spreading.
- Automatically detect locomotive derailing, and perform emergency control.
Basic Specification
Items |
Specifications |
Options |
---|---|---|
Type of vehicle |
Diesel electric locomotive (AC-AC type) |
– |
Operation form |
Manual operation in control platform, Remote operation by wireless transmitter |
– |
Operation maintenance weight |
80 ton |
60 ton |
Maximum traction weight |
2,400 ton (normal 600ton or 1,200 ton) |
1,800 ton |
Maximum operation speed |
20km/h |
60km/h |
Car body dimensions |
13,100(L) X 2,750(W) X 3,800(H)mm |
– |
Track gage |
1,067mm 1,435mm 1,676mm |
Option available |
Minimum curve radius |
60mR |
– |
Drive engine generator output |
400kVA class |
– |
Auxiliary engine generator output |
13kVA class |
– |
Drive motor rated output |
60kW X 4 |
– |
Fuel tank capacity |
2,000 liter |
– |